Almost all the electronic circuits mentioned in this site are designed and built on a PCB board. But you cannot build these electronic circuits if you do not know the basics of soldering. If you do not know to solder well, the solder joints will not be perfect and thus the circuit will have serious flaws. In this post, we will discuss about the soldering tools or soldering kits that are used for this purpose. We will also have a step by step procedure on how to solder a circuit board.
Soldering Tools
The basic tools that are used for this purpose are
- Soldering Iron
- Solder Wire [Alloy]
- Flux
- PCB and the components that are to be soldered
The soldering iron is the heat source tool for the process. It should be of high quality. Of course the price may increase with the quality, but the soldering will be perfect. Usually a 25 Watt soldering iron is adequate for the process. A higher watt device may bring too much heat to the PCB and will surely damage the sensitive components. A lesser watt device may not have adequate heat and thus is prone to be extensively used. This may also cause extensive heat damage.
The solder wire is used to fix the components like resistors, capacitors and so on to the PCB in the given fields. The leads of the devices are connected to the track of the PCB by melting the soldering wire to the junction. When the heat from the soldering iron touches the soldering wire it starts melting and this melted wire when introduced to the junction, joins the components to the track firmly.
The soldering wire is actually an alloy of tin and lead in the ratio 60:40. This is the best ratio that is considered for soldering in PCB’s. There are other proportions of this alloy and they are considered low quality as the tin content with respect to lead will be lower.
A high quality solder wire will have a melting point of about 250 degree Celsius and will have a very high conductivity along with a shiny appearance. When a high quality solder wire is used to connect the components to the PCB, there is to be no fear of corrosion in future.
Flux is another important component that is used in soldering purposes. It is sealed to the core of the solder wire before soldering. The flux is used to reduce the surface tension of the solder wire in its melting point. Thus, it acts as a wetting agent and wets the parts that are to be joined to the PCB. This also helps in the proper heat transfer from the solder iron to the solder wire.
Another main use of the flux is to prevent oxidation of both the solder wire and the components that are added to the PCB. The Tin-Lead alloy that is used as solder wire may have no problem when attached to copper. But they do not attach so well, when in contact with the oxides of copper. The oxides of copper mostly form when the temperature is increased for soldering. The flux can prevent the formation of metal oxide as they are nearly inert at room temperature and become strongly reduced when the temperature increases. The use of flux causes the rise of smoke when the soldering process continues. During this time the flux acts as a catalyst and helps in removing the oxidants and thus cause a better solder joint.
Soldering Technique
If you are a beginner, your initial soldering results may be just average and unprofessional in looks. You can only master the technique by practice. Here is the step by step procedure for soldering.
- First of all keep the solder iron plugged in for about a minute and a half before starting to use it. By that time the solder iron may get heated to the optimum temperature [250 degree Celsius].
- Bend the leads of the different devices that are to be connected to the PCB. For a clean bend, the approximate distance of bend is about 2mm from its body ends.
- If you are connecting a resistor to the PCB, find its spot and place it into the hole of the PCB.
- After placing the resistor flip the PCB in such a way that the inserted leads looks towards you.
- Take the soldering iron in the right hand and the solder wire in the left hand. The solder wire must be placed on your finger tips with about 3 inches extending from your finger grip.
- Bring both the solder iron tip and the solder wire tip close to the base of the lead of the resistor and copper track of the PCB. Make them come in contact at the same instant at the junction.
- You will notice that the solder wire starts to melt as soon as the contact is made.
- When the wire starts melting keep pushing it till the joint has been filled up with the molten alloy.
- Move away the solder wire and the solder iron simultaneously and allow the molten wire to solidify. Thus one lead of the resistor has been connected to the PCB. Do the same step for the other lead and also for all other components.
The setp by step procedure is also shown in the figures given below.
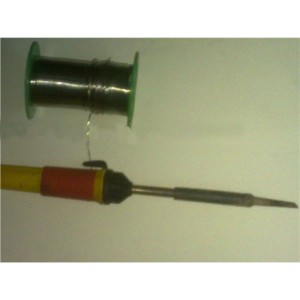
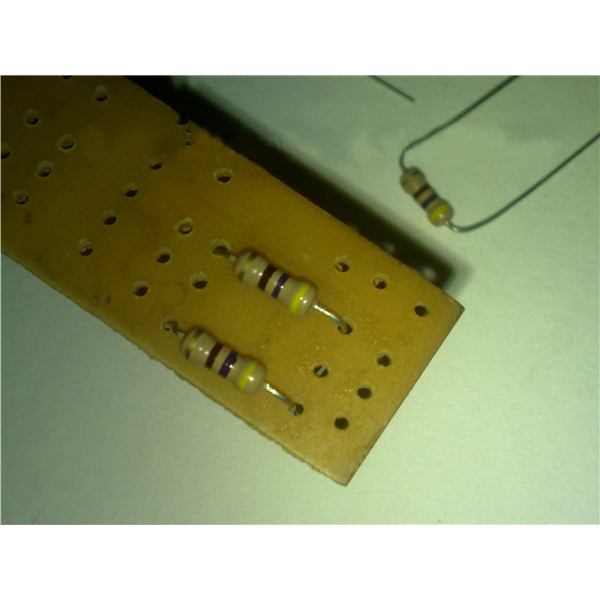
Precautions to be taken while Soldering
For a good heat transfer, the solder wire and the solder iron must be well cleaned before starting. It must also be pre-tinned with solder. In order to avoid the overheating of PCB, the components are usually elevated above the PCB. After the component is inserted in the PCB hole, the excess lead is cut off, thus leaving a length of about the radius of the pad.
After soldering, the soldered joints must also be cleaned after it has been solidified.
Some components that are to be soldered may be heat sensitive. For such components a heat sink may be used on the leads which will reduce the heat transfer to the components. The only problem is that for such components more heat will be required from the solder iron to complete the joint.
De-soldering and Re-soldering
There may be cases where a soldered PCB may be taken for re-soldering. The problem is that the solder that is already used has some dissolved base metals that make it unfit for reuse. If you try to re-solder onto it, the new solder will not properly bond with the base metal and will cause the formation of a brittle cold solder joint with a crystalline appearance.
So before re-soldering it is good practice to de-solder and thus remove the solder from the joint. For this purpose there are de-soldering equipments called solder suckers. By doing this a lot of flux is released which will clear the dissolved base metals and all other contaminants from the copper trace. Thus a bright, shiny, clean junction will be ready to be re-soldered.
Take a look at the post below to know the exact method of desoldering.
TAKE A LOOK : HOW TO DESOLDER ELECTRONIC CONNECTIONS
Soldering – Video
14 Comments
thanks guys this is realy good stuf.
A convex finish of the joint indicates the solder is adhering to either component lead or the copper track only, called dry joint, will spoil the performence of the equipment or damage it.
If it is shinny and concave in finish it is the best soldering. Preheating the track and the component lead is a must before proceeding with feeding of solder wire.
The following site gives the best practical view.
http://www.technologystudent.com/pcb/solder1.htm
Thats is good professional engineer not apprentice.